- Need Free Consultation ?
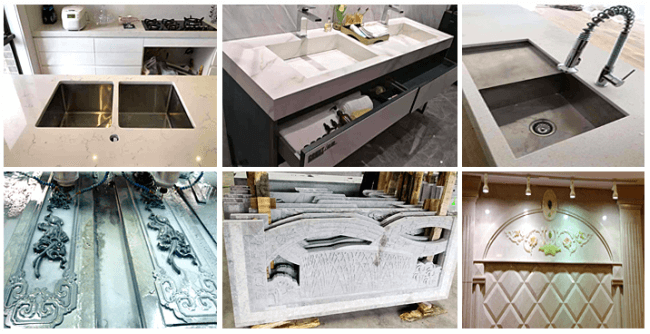
Applications
CNC Marble
Versatile Applications of CNC Stone and Metal Engraving Machines:
Granite Engraving: Capable of engraving detailed designs on granite and other hard stones up to 3mm thick, offering precision and durability for intricate stonework.
Marble Engraving and Cutting: Efficiently engraves and cuts marble, providing high-quality results for both decorative and functional applications.
Bluestone Processing: Ideal for engraving and cutting bluestone, delivering accurate and consistent results for various architectural and design projects.
Sandstone Engraving: Suitable for engraving sandstone, enabling the creation of detailed patterns and designs with high precision.
Glass Engraving: The machine can also be used to engrave glass, allowing for customized glass designs and applications.
Metal Aluminum Profiles: Capable of milling metal aluminum profiles, offering precise and clean cuts for various industrial and manufacturing needs.
Thin Copper Milling: Efficiently mills thin copper, making it suitable for applications that require fine and accurate metalwork.